Steam Ejector Sizing Guide
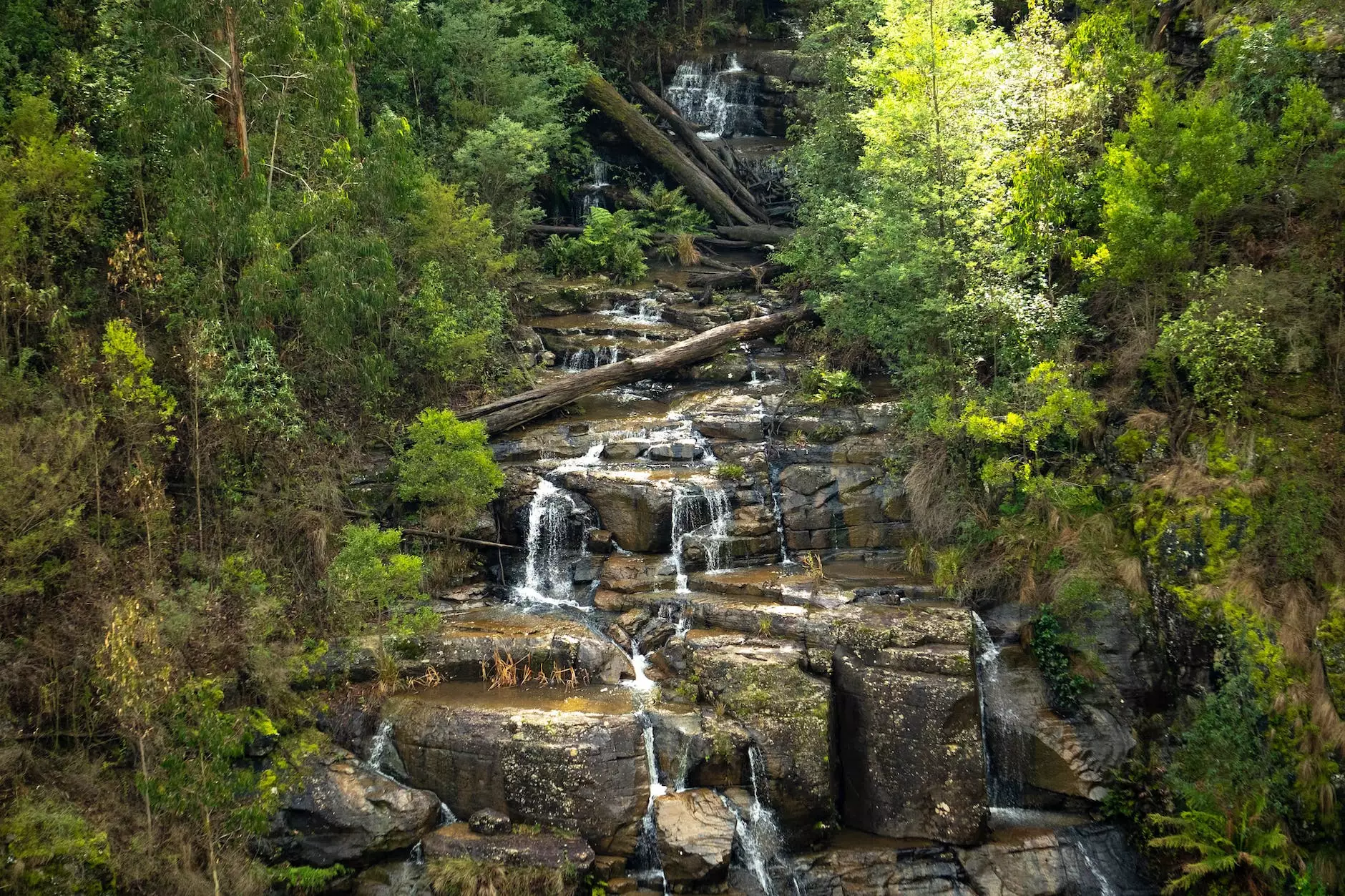
Introduction
Welcome to Ezejector.com, your ultimate resource for steam ejector sizing. In this comprehensive guide, we will provide you with everything you need to know to effectively size steam ejectors for your business. Whether you are new to steam ejectors or looking to optimize your existing system, our aim is to equip you with the knowledge and techniques that will help you make informed decisions.
Understanding Steam Ejectors
Before we dive into the intricacies of steam ejector sizing, let's take a moment to understand what they are and how they work. At its core, a steam ejector is a device that uses steam pressure to create a vacuum by entraining and compressing the gas or vapor present in a process. It offers significant advantages such as energy efficiency, low maintenance requirements, and reliable operation.
The Importance of Proper Sizing
Proper sizing of steam ejectors is crucial to achieving optimal performance and efficiency. An undersized ejector may not be able to achieve the desired vacuum level, leading to reduced productivity and increased energy costs. On the other hand, an oversized ejector may result in unnecessary capital expenditure and excessive operating costs. It is, therefore, essential to strike the right balance and select the right ejector size for your specific application.
The Sizing Process
The process of steam ejector sizing involves several key factors that need to be considered. Here, we outline the essential steps:
Step 1: Define your Requirements
Before diving into the technical aspects, it is essential to clearly define your requirements. Determine the desired vacuum level, process parameters, capacity, and any specific industry standards that need to be met. This will serve as the foundation for the sizing process.
Step 2: Gather Process Data
To accurately size steam ejectors, gather relevant process data such as flow rates, temperatures, pressures, and composition of gases or vapors. A comprehensive understanding of your process helps in selecting the right ejector configuration and optimizing its performance.
Step 3: Perform Calculations
Based on the gathered data, perform the necessary calculations to determine the required ejector size. Factors such as motive steam pressure, nozzle design, diffuser efficiency, and back pressure should be accounted for to ensure accurate sizing.
Step 4: Evaluate Operating Conditions
Consider the operating conditions specific to your application, including altitude, temperature variations, and other environmental factors. These factors can affect the performance of the steam ejector and may necessitate adjustments during the sizing process.
Step 5: Assess Practical Limitations
While technical calculations provide a foundation, it is crucial to assess any practical limitations that might impact the implementation of the selected ejector size. Factors like available space, maintenance accessibility, and cost considerations should be taken into account.
Common Challenges in Steam Ejector Sizing
Steam ejector sizing can present unique challenges depending on the specific application. Let's take a look at some common hurdles:
High Operating Temperatures
In applications where high operating temperatures are involved, proper material selection becomes critical. The steam ejector design should account for thermal expansion, corrosion resistance, and heat conduction to ensure reliable and safe operation.
Varying Process Conditions
When process conditions vary significantly, it is important to consider the range and impact of these variations on the ejector's performance. Ensuring flexibility in the ejector design and selecting appropriate control mechanisms can help maintain optimal performance throughout the operational range.
Non-Ideal Gases or Vapors
In cases where the gases or vapors being handled are non-ideal, accurate characterization becomes essential. Factors like compressibility, heat capacity, and molecular weight should be considered to ensure accurate steam ejector sizing.
Expert Tips for Effective Steam Ejector Sizing
Here are some expert tips to optimize your steam ejector sizing process:
1. Collaborate with Experts
Consult with experienced professionals who specialize in steam ejector systems. Their expertise and knowledge will help you navigate complex challenges, avoiding common pitfalls and ensuring accurate sizing.
2. Utilize Advanced Simulation Tools
Leverage advanced simulation tools to model and analyze the performance of steam ejectors under different operating conditions. These tools provide valuable insights, allowing you to make informed decisions based on accurate simulations.
3. Stay Up-to-Date with Industry Developments
The field of steam ejectors is constantly evolving, with new technologies and methodologies emerging. Stay connected with industry developments, attend conferences, and engage in knowledge-sharing platforms to stay at the forefront of steam ejector sizing techniques.
Conclusion
Sizing steam ejectors is a critical process that directly impacts the efficiency and performance of your operations. By following the steps outlined in this guide and considering the expert tips, you can ensure accurate sizing and reap the benefits of optimized steam ejector systems. At Ezejector.com, we are committed to providing comprehensive resources and expert guidance to help businesses succeed in their steam ejector sizing endeavors.
This article is authored by Ezejector.com