The Rise of CNC Turning Parts Factories: A New Era in Metal Fabrication
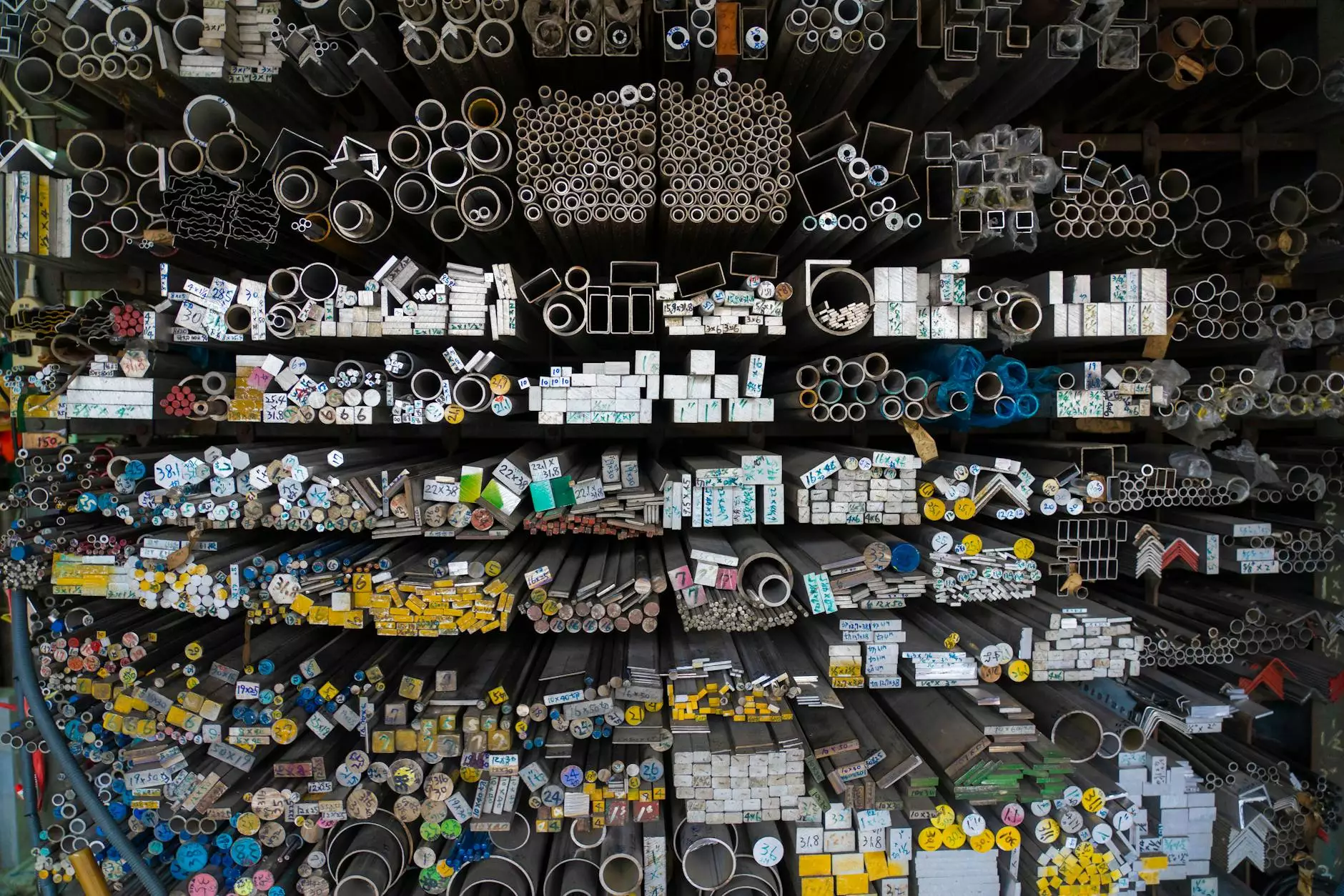
The manufacturing landscape has evolved tremendously in recent years, and at the forefront of this evolution are CNC turning parts factories. These innovative facilities leverage advanced technology to produce high-precision components for various industries. With the demand for bespoke parts on the rise, understanding the significance of these factories becomes vital for businesses seeking to stay ahead in a competitive market.
Understanding CNC Turning: A Brief Overview
CNC, or Computer Numerical Control, refers to the automated control of machining tools by means of a computer. When it comes to turning processes, CNC machines are designed to rotate a workpiece against a cutting tool to shape it into the desired form. This technology not only enhances precision but also significantly increases production efficiency.
The Significance of CNC Turning Technology
CNC turning technology has revolutionized the way components are produced. Here are some key benefits:
- Precision and Accuracy: CNC machines can create parts with minimal tolerances, ensuring high-quality output with every cycle.
- Efficiency: Automated systems operate continuously and can produce complex parts without the need for constant human intervention.
- Versatility: CNC machines can work with various materials, including metals, plastics, and composites, making them suitable for numerous applications.
- Cost-Effectiveness: While the initial investment in CNC technology may be high, the long-term savings from reduced labor costs and minimized waste are significant.
Inside a CNC Turning Parts Factory
CNC turning parts factories are equipped with a variety of machineries, such as lathes, milling machines, and grinders, all controlled by sophisticated computer systems. These factories typically follow a streamlined process to ensure that every step from design to production is optimized for quality and efficiency.
The Production Process
The typical production process in a CNC turning parts factory includes the following stages:
- Design: Engineers use CAD software to create detailed designs of the desired components.
- Programming: The designs are then translated into CNC programming code, often using G-code.
- Setup: Machines are set up with the necessary tools and the workpiece material.
- Machining: The CNC machine begins the turning process, adhering to the programmed specifications.
- Quality Control: Finished parts undergo rigorous testing to ensure they meet predefined quality standards.
- Finishing: Additional processes such as coating or polishing may be applied to enhance the final product.
Quality Assurance in CNC Turning Parts Factories
In an industry where precision is paramount, quality assurance is a critical element that sets top-performing CNC turning parts factories apart from their competitors. Factories implement various quality control measures to guarantee that each part fulfills the required specifications.
Quality Control Measures
- Dimensional Inspection: Utilization of advanced measuring tools, such as calipers and CMM (Coordinate Measuring Machines), ensures parts are manufactured to exact dimensions.
- Material Testing: Testing the raw materials for their mechanical properties before production helps prevent potential defects.
- Continuous Monitoring: Real-time monitoring of machinery operations helps identify issues early in the production process.
- Feedback Loops: Implementing systems for feedback allows for continuous improvement in production methods and outcomes.
Applications of CNC Turning Parts
The versatility of CNC turning parts facilitates their usage across various industries. Here are some notable applications:
- Aerospace: CNC turning plays a vital role in the production of highly intricate turbine components and structural parts.
- Automotive: The automotive industry relies heavily on CNC turning for manufacturing high-performance engine components, transmission parts, and more.
- Medical Devices: Precision parts for medical equipment, such as surgical instruments and implants, are often made using CNC turning technology.
- Electronics: Components that require high levels of accuracy and reliability, such as connectors and housings, benefit from CNC turning processes.
Why Choose DeepMould for Your CNC Turning Needs?
As manufacturers look for reliable suppliers, DeepMould.net stands out in the realm of metal fabrication, particularly in the production of CNC turning parts. Here’s why:
Expertise and Experience
With years of experience in the industry, DeepMould has cultivated a wealth of knowledge about CNC processes. Our team of skilled engineers and technicians works diligently to ensure that every product meets the highest standards of quality.
State-of-the-Art Technology
Equipped with cutting-edge CNC machinery and software, DeepMould utilizes the latest innovations to deliver exceptional results. Our technology enables us to handle complex designs and high-volume production runs with ease.
Commitment to Quality
Quality is at the heart of DeepMould’s operations. We implement stringent quality control measures to ensure that every part is not only produced efficiently but also meets our clients' exact specifications.
Custom Solutions
At DeepMould, we understand that each client has unique requirements. We offer customized solutions tailored to your specific needs, from initial design consultations to final part production.
Conclusion: The Future of CNC Turning Parts Factories
As industries continue to advance, the role of CNC turning parts factories becomes more significant. These factories not only enhance manufacturing efficiency but also pave the way for innovative designs and superior quality assurance. Choosing a competent partner like DeepMould can provide businesses with the competitive edge needed in today’s dynamic market.
Embrace the future of manufacturing, and ensure your business stands out by investing in quality CNC turning parts. Contact DeepMould today for more information on how we can support your manufacturing needs.