Unlocking the Potential of Die Casting and Injection Moulding in Metal Fabrication
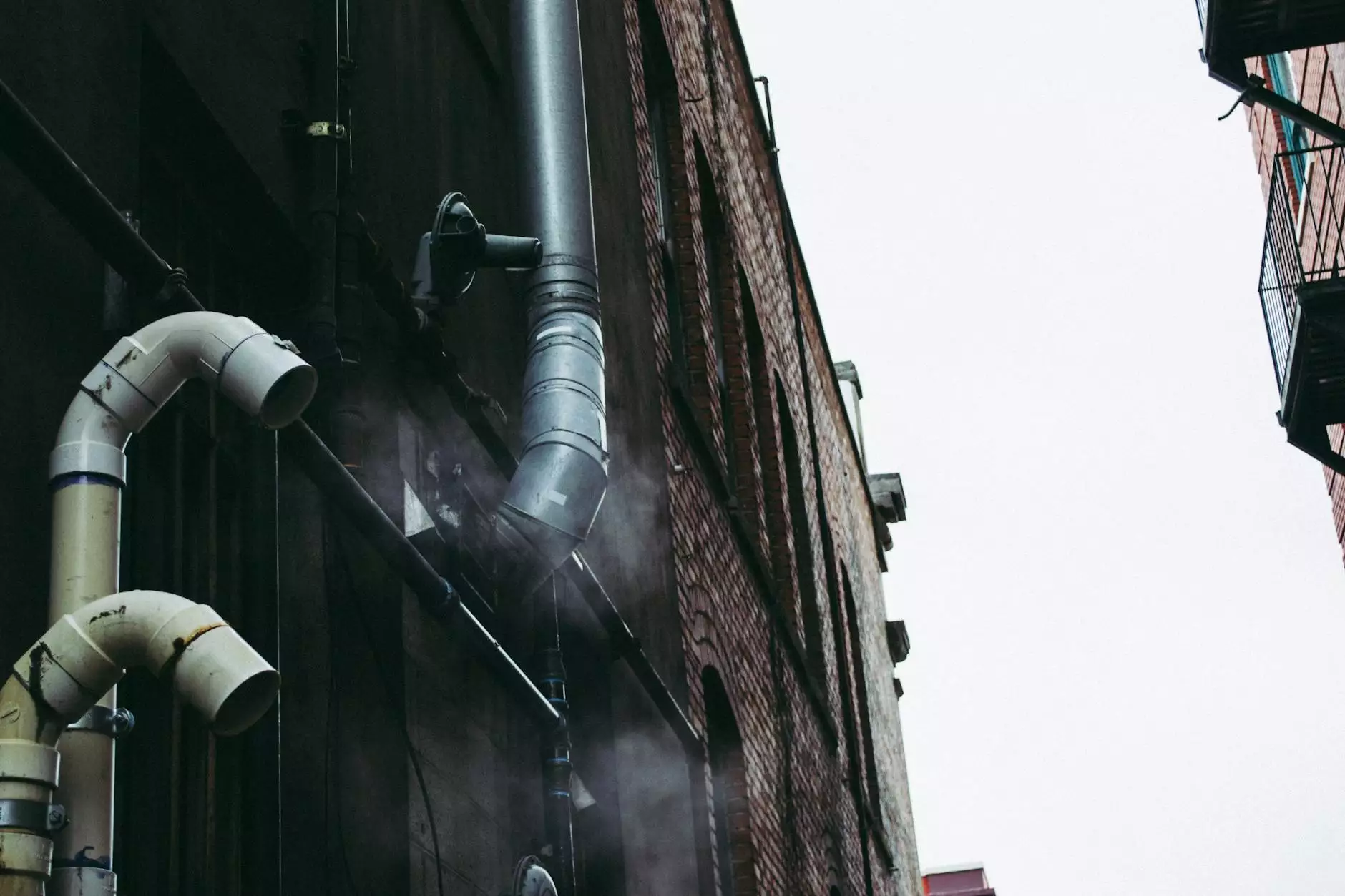
In the realm of metal fabrication, two processes stand out as cornerstones of efficiency and innovation: die casting and injection moulding. These methods not only streamline production but also enhance the quality of the end products. For businesses looking to optimize their manufacturing processes, understanding these techniques and their applications is crucial. In this article, we will delve deep into the intricacies of die casting and injection moulding, highlighting their unique advantages, differences, and ideal applications in today’s manufacturing landscape.
Understanding Die Casting
Die casting is a versatile and widely used manufacturing process that involves forcing molten metal under high pressure into a mold cavity. The result is a highly accurate and intricately shaped metal part, suitable for various applications.
The Die Casting Process
- Preparation: Start by preparing the molten metal, which is typically an alloy such as aluminum, zinc, or magnesium.
- Injection: The molten metal is injected into a pre-made mold at high pressure, ensuring that every detail of the design is captured.
- Cooling: After the metal has filled the mold, it is allowed to cool and solidify, forming the final product.
- Ejection: Once cooled, the die is opened, and the newly formed part is ejected from the mold.
Key Benefits of Die Casting
- Excellent surface finish: Die-cast products typically feature a smooth surface and precise dimensions, reducing the need for additional machining.
- High production rates: The efficiency of die casting enables mass production of thousands of parts in a relatively short time.
- Design flexibility: Complex designs can be achieved with fine detail, greatly expanding the design possibilities for manufacturers.
- Material efficiency: Minimal waste is produced because of the ability to recycle unused metal and the high accuracy of mold designs.
Exploring Injection Moulding
Injection moulding, while often associated with plastics, can also be applied to metals in a similar fashion. This process involves injecting molten material into a mould—a practice that has revolutionized how a variety of products are manufactured.
The Injection Moulding Process
- Material Selection: Choose the appropriate material based on required properties, which may include thermoplastics, thermosets, or metal powders for metal injection moulding.
- Heating: The plastic or metal is heated until it becomes pliable or molten.
- Injection: The material is injected into a mold cavity under controlled pressure and temperature.
- Cooling: The material is allowed to cool, solidifying into the desired shape.
- Ejection: The mold opens, and the final part is ejected.
Key Benefits of Injection Moulding
- High efficiency: Like die casting, injection moulding can produce a large number of parts in a short period.
- Versatile materials: A range of materials can be utilized in injection moulding, allowing for great adaptability in product design.
- Low scrap rates: The process generates minimal waste, making it an environmentally friendly choice and allowing for cost-effective manufacturing.
- Complex geometries: Deep undercuts and intricate designs can be achieved, broadening the scope for product design.
Comparative Analysis of Die Casting and Injection Moulding
While both die casting and injection moulding serve similar purposes in creating intricate metal parts, they differ in several ways:
FeatureDie CastingInjection MouldingMaterial TypesPrimarily metals (aluminum, zinc, magnesium)Primarily plastics and metal powdersProduction VolumeHigh volume, low-cost componentsScales well from low to high volumeSurface FinishExcellent finish, often requires little post-processingVaries depending on the material and processComplexity of DesignHighly detailed designsAllows for complex geometries, more flexibility in designCostInitial tooling costs can be high but amortized over large production runsLower initial costs for small-scale productionApplications of Die Casting and Injection Moulding
The applications of die casting and injection moulding are incredibly vast and span numerous industries:
Industries Using Die Casting
- Automotive: Components such as engine blocks, transmission cases, and housings.
- Electronics: Housings for various electronic devices which require lightweight and durable materials.
- Aerospace: Critical parts that must withstand extreme conditions.
- Consumer Goods: Items like kitchenware and outdoor equipment.
Industries Using Injection Moulding
- Packaging: Containers, bottles, and caps that require versatility in design.
- Medical Devices: Precision parts for medical tools that necessitate stringent hygiene standards.
- Consumer Electronics: Cases for smartphones, laptops, and other handheld devices.
- Automotive: Interior and exterior trim components that benefit from lightweight and durable plastic materials.
Future Trends in Die Casting and Injection Moulding
The future of die casting and injection moulding is shaped by technological advancements and innovations:
Advancements in Materials
As industries demand stronger, lighter, and more durable materials, the development of new alloys and polymers continues to expand the horizons of die casting and injection moulding.
Automation and Robotics
Embracing automation can enhance efficiency, precision, and safety in manufacturing processes. Integrating robotics for handling, inspection, and part production will undoubtedly lead to reduced cycle times and improved accuracy.
Sustainable Practices
The increasing focus on sustainability in manufacturing is leading companies to adopt more environmentally friendly processes. This includes reducing scrap rates, reusing materials, and utilizing energy-efficient machinery. Countless manufacturers are investing in recycling infrastructures to recycle scrap and unused metal.
Industry 4.0 and IoT
The advent of Industry 4.0 and the Internet of Things (IoT) is transforming production facilities by introducing smart technologies and data analytics for better decision-making and predictive maintenance. These technologies allow for more streamlined operations, reducing downtime and increasing productivity.
Final Thoughts
In the competitive landscape of metal fabrication, the integration of die casting and injection moulding technologies can significantly enhance a company’s capabilities and efficiency. Understanding these manufacturing processes is essential for businesses aiming to innovate and stay ahead in the market. By leveraging the advantages of both techniques, organizations can produce superior products that meet the ever-evolving demands of their consumers. As we move forward, the continuous evolution of materials, automation, and sustainable practices will determine the future trajectory of die casting and injection moulding, offering exciting new possibilities for manufacturers worldwide.
For more insights and a comprehensive overview of the latest developments in the metal fabrication industry, visit us at deepmould.net.