The Comprehensive Guide to Injection Molding Plastics
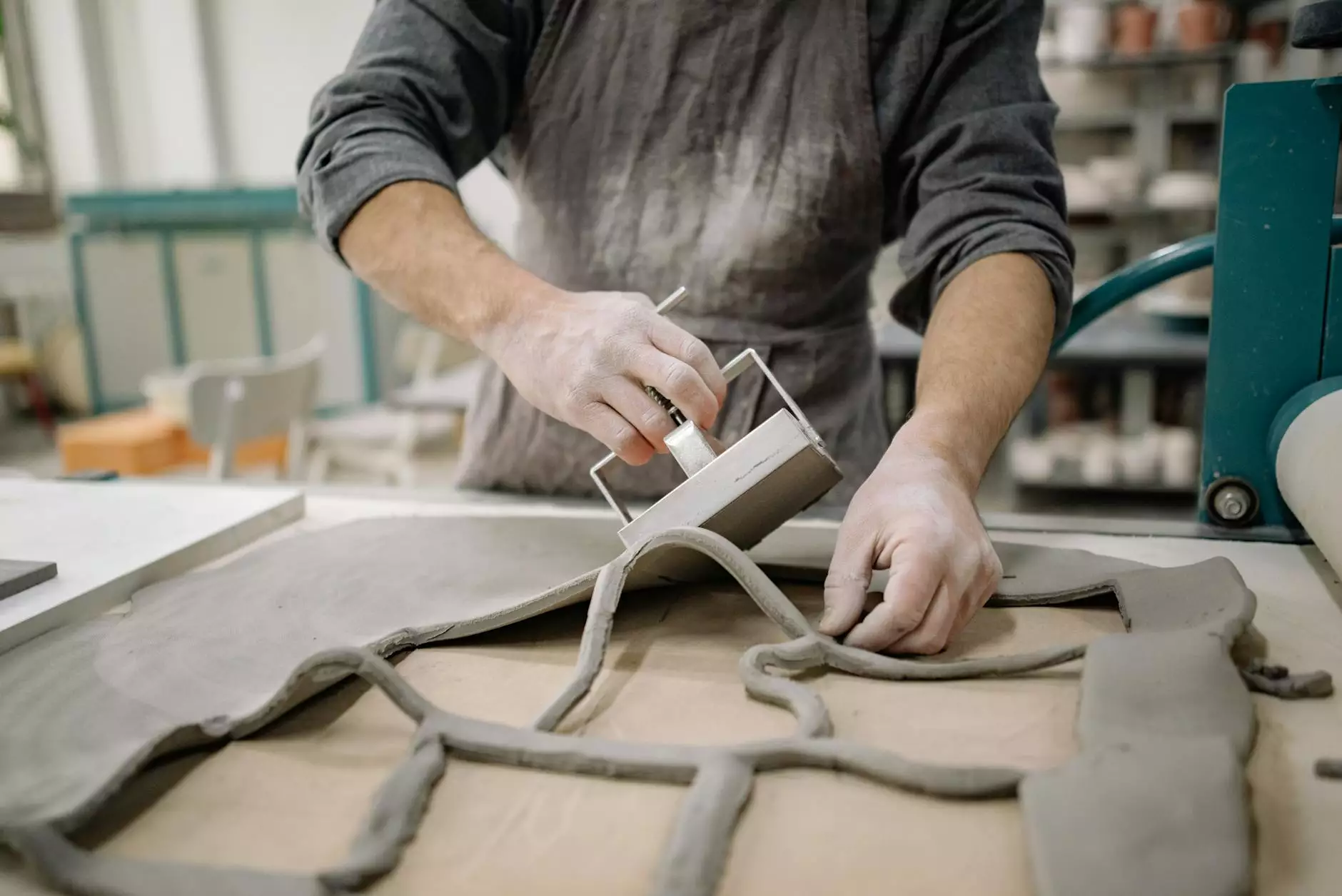
Injection molding plastics is a cornerstone of modern manufacturing, revolutionizing how we produce plastic components across various industries. From automotive to consumer products, this process allows for the efficient creation of complex shapes and high volumes of production. In this article, we will delve deep into the intricacies of injection molding plastics, exploring its benefits, applications, and the future of this essential manufacturing technique.
What is Injection Molding?
Injection molding is a manufacturing process used for producing parts by injecting molten material into a mold. This method is commonly used for plastics but can also incorporate metals and other materials. The process begins with a heated barrel where the plastic pellets are melted down. Once the desired temperature is reached, the molten plastic is injected into a customized mold at high pressure, where it cools and solidifies into the final shape.
Advantages of Injection Molding Plastics
Injection molding plastics offers numerous advantages that make it a preferred method in the manufacturing industry:
- High Efficiency: The ability to produce large volumes of parts quickly and consistently.
- Precision: Molds can be designed with high levels of accuracy, ensuring a perfect fit and finish.
- Versatility: A wide range of materials can be used, providing flexibility in product design.
- Minimal Waste: The process generates very little scrap material, making it an environmentally friendly option.
- Cost-Effectiveness: Although initial setup costs can be high, the long-term savings in labor and materials are significant.
Applications of Injection Molding Plastics
The applications of injection molding plastics are vast, touching nearly every sector of the economy:
1. Automotive Industry
Injection molded components are critical for automobiles, providing everything from dashboard panels to internal mechanisms. The lightweight nature of plastics contributes to fuel efficiency, while their durability ensures long-lasting performance.
2. Consumer Goods
Everyday products, such as toys, kitchenware, and personal care items, often utilize injection molding. The process allows for intricate designs and vibrant colors that appeal to consumers.
3. Electronics
From mobile phone casings to intricate circuit boards, injection molding plastics is essential in producing electronic devices. The precision and customization available through this process ensure that electronic components work seamlessly together.
4. Medical Devices
The medical field benefits significantly from injection molding, as it allows for the production of precise and sterile components such as syringes, IV bags, and surgical instruments. The high standards of quality control ensure that these products meet strict regulatory demands.
Types of Injection Molding Processes
Several methods exist within the realm of injection molding plastics, each with its unique benefits:
- Standard Injection Molding: The most common method used in various industries for mass production.
- Gas-Assisted Injection Molding: Uses gas to hollow out parts, reducing weight and material use.
- Structural Foam Molding: Combines solid and foamed materials for added strength at a reduced weight.
- Two-Shot Molding: Produces two different materials in one mold, allowing for complex textures and colors.
- Insert Molding: Involves placing a material (like metal) into a mold, then injecting plastic around it, enhancing the part's strength.
Understanding the Injection Molding Process
The injection molding process can be broken down into several key stages:
1. Material Preparation
The first step involves preparing the plastic pellets, which are fed into a hopper. The pellets are typically made from thermoplastics or thermosetting polymers, and selecting the right material is crucial for the application's demands.
2. Injection Phase
In the injection phase, the heated barrel melts the plastic, allowing it to be injected into the mold. This step requires high pressure to ensure that the molten plastic fills all areas of the mold effectively.
3. Cooling Phase
Once the mold is filled, it is allowed to cool. This step is important as it solidifies the plastic and defines the product's shape. The cooling time can vary based on the size and complexity of the part being produced.
4. Ejection Phase
After cooling, the mold opens, and ejector pins push the finished part out. This phase must be carefully controlled to prevent damage to the part or the mold.
5. Finishing Operations
Once ejected, the parts may go through additional processes such as trimming, painting, or assembly before being packaged and shipped.
Choosing the Right Material for Injection Molding Plastics
Selecting the appropriate material is vital for the success of any injection molding plastics project. Some common materials include:
- ABS (Acrylonitrile Butadiene Styrene): Known for its toughness and impact resistance, often used in consumer goods and automotive components.
- PP (Polypropylene): A low-cost material that exhibits chemical resistance, making it ideal for packaging and automotive parts.
- PA (Nylon): Offers excellent wear resistance and mechanical strength, suitable for industrial applications.
- PVC (Polyvinyl Chloride): Commonly used in plumbing, electrical, and construction materials for its durability.
Challenges in Injection Molding Plastics
Despite its many benefits, injection molding plastics is not without challenges. Some common issues include:
- Mold Design: A poorly designed mold can lead to defects in the final product, necessitating skilled engineers to create effective designs.
- Material Selection: Choosing the wrong material can result in part failure and increased costs.
- Cycle Time: Reducing cycle time while maintaining quality is a constant challenge for manufacturers.
- Environmental Concerns: The production and disposal of plastic raise environmental issues, making sustainability a critical focus area.
Future Trends in Injection Molding Plastics
The future of injection molding plastics is bright, with several exciting trends emerging:
1. Sustainable Practices
As companies face increasing pressure to adopt sustainable practices, the injection molding industry is investigating bioplastics and recycled materials as alternatives to traditional plastics.
2. Advanced Technologies
Technological advancements such as 3D printing are beginning to blend with injection molding techniques, enabling faster prototyping and customization of designs.
3. Smart Manufacturing
With the rise of Industry 4.0, smart sensors and automation are being integrated into injection molding processes, improving efficiency and reducing waste.
Conclusion
In summary, injection molding plastics represents a dynamic and vital aspect of modern manufacturing. Its advantages, from high efficiency to cost-effectiveness, make it an invaluable technique across numerous industries. As we look to the future, embracing sustainability and innovation will ensure that injection molding continues to thrive and adapt to the evolving demands of the marketplace.
For businesses looking to leverage injection molding plastics for their manufacturing needs, partnering with experienced companies such as DeepMould.net can provide the expertise and resources necessary to excel in this competitive landscape.